Maintaining the hydraulic station of a block making machine is essential to ensure stable pressure, smooth motion, and long-term reliability. Below is a practical maintenance guide specifically for the hydraulic system:
Hydraulic Station Maintenance Checklist
✅ Daily Checks
1. Oil Level Check
• Ensure the hydraulic oil level is between the min and max marks on the tank.
• Top up with the correct hydraulic oil if low.
2. Leak Inspection
• Visually check all hoses, connectors, and fittings for oil leaks.
• Tighten fittings or replace damaged hoses immediately.
3. Temperature Monitoring
• Ensure the oil temperature remains within the recommended range (usually 35–55°C).
• Overheating can cause viscosity breakdown and damage seals.
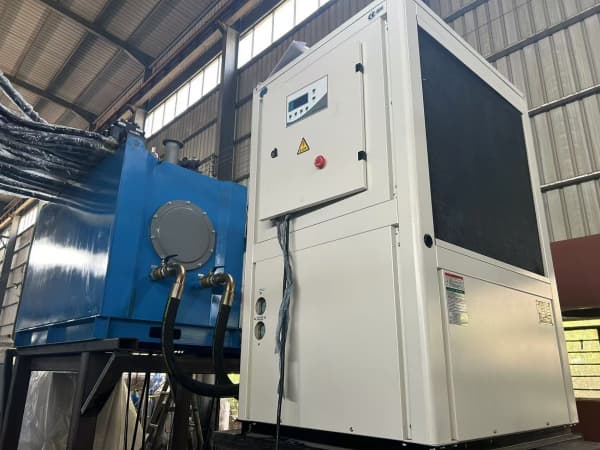
✅ Weekly Maintenance
1. Clean the Oil Filter (if reusable)
• Remove and clean the return or suction filter with diesel or kerosene, then dry it before reinstalling.
2. Check Pressure Settings
• Verify that the system pressure (e.g., main relief valve) is within specified limits.
• Use a pressure gauge at key test points.
3. Examine Pump Noise & Vibration
• Listen for unusual noise (grinding, whining) from the hydraulic pump—could indicate cavitation or air bubbles.
• Check for excessive vibration; tighten mounting bolts or realign if needed.
✅ Monthly Maintenance
1. Inspect Oil Quality
• Take a small sample of oil:
• If it’s dark, smells burnt, or contains particles, it needs replacing.
• Send for lab analysis if necessary (for large operations).
2. Clean Hydraulic Tank Breather Cap
• A blocked breather can cause pressure build-up and contamination.
3. Check Cylinder and Valve Movement
• Ensure cylinders extend/retract smoothly and solenoid valves switch correctly.
• Test emergency stop functions.
✅ Every 6 Months or 1000 Hours
1. Replace Hydraulic Oil
• Drain old oil completely, flush the tank with light oil or flushing fluid, and refill with fresh oil.
• Clean or replace return/suction filters.
2. Inspect and Replace Seals
• Check for oil leaks around cylinder seals and pump shaft seals.
• Replace any worn seals to prevent pressure loss.
3. Electrical Component Check
• Inspect solenoid coils, connectors, and relays.
• Tighten terminals and clean contact points.
�� Tools and Materials Needed
• Pressure gauge set (with quick couplers)
• Oil suction pump or extractor
• Clean rags, oil pans, and funnel
• Spare filters, seals, and O-rings
• Hydraulic oil (as per manufacturer spec)